 |
|
Recycling Systems |
|
This section contains the RGF line of wash water recycling equipment. RGF utilizes 40 technologies to develop industry specific water recycling systems. RGF is the recognized industry leader with thousands of systems installs worldwide.
Industrial water recycling has been one of the main mission of RGF since its inception in 1985. Water recycling is an industrial priority for the following reasons: |
|
Cost |
RGF recycle system will remove contaminants while leaving in the dissolved cleaning agent, thereby not only are you saving water, but also saving cleaning detergents. By recycling wash water and cleaning agents, studies have shown saving at typical trucking firms over
discharging to sewer. |
|
|
Compliance |
By recycling, you will avoid possible fines, regulatory litigation, negative publicity and civil litigation. |
|
|
Positive Image |
Companies that are environmentally conscious are viewed upon by employees and customers as forward thinking, positive performers and professionals who carry an image that advertising cannot buy. |
|
|
Regulations |
By recycling, you avoid regulatory monitoring of your waste stream, thereby reducing visits to your site by regulatory auditors. |
|
|
Moral |
By recycling, you will be saving hundreds of thousands of gallons of water, our most precious resource, which we are grossly mismanaging. |
|
|
Fresh Water Available vs. Population Growth |
|
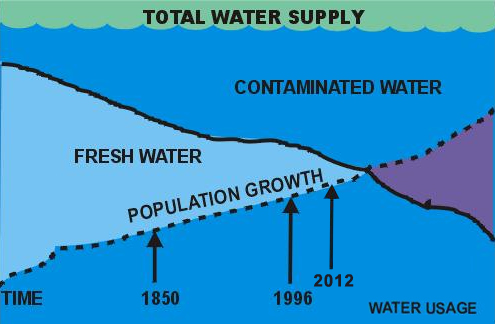 |
|
Recycling can no longer be viewed as a necessary evil. It
should be viewed as a variable cost reduction program and positive public relations vehicle. |
|
|
WashMaster Universal |
|
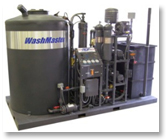 |
|
TheWashMaster Universal is a single skid mounted system designed for complete “plug and go” applications. The WashMaster Universal also includes our oil water separation technology for all applications other than turf where hydrocarbon removal is required. |
|
Specifications |
|
Flow Rate |
20 g.p.m. |
Final Filtration |
1 Micron |
Process Water Storage |
550 gallons |
Dimensions |
5' W X 10' L X 7' H |
System Capacity |
800 gallons |
Process Flow Rate |
20 g.p.m |
Filter Backflush |
Automatic |
CO3P Oxidation System |
SM UV/O3 Chamber |
|
|
Applications |
Standard Features |
|
Military Bases |
Hydrocarbon Accumulator |
City/ County Transportation |
CFC System |
Waste Haulers |
Process Pump |
Equipment Rental Companies |
Supply Pump |
Car, Truck & Tractor Repair Shops |
Std. Multi-Media Filter |
Municipal and State Garages |
Auto Filter Backflush System |
Bus Companies |
Polishing Filtration System |
Construction Companies |
SM-CO3P Catalytic Oxidation |
|
|
BIOLOGICAL TREATMENT SYSTEMS |
There are two basic biological treatment processes: aerobic (with oxygen) and anaerobic (without oxygen). |
Aerobic Treatment is the process by which microorganisms use the waste’s organic component with oxygen, which produces cell growth and end products of carbon dioxide and water. The most popular is the activated sludge process which is commonly used for domestic and industrial wastewater. This process provides a high quality effluent and is capable of reducing B.O.D by 95%. The bacterial process oxidizes the soluble and suspended organic to carbon dioxide and water in the presence of oxygen. The organic material is converted into new cells or used to support growth of existing cells. The excess of cells is sludge. |
Anaerobic Treatment is the process where microorganisms convert organic compounds to methane, carbon dioxide, cellular materials, and other organic compounds. The anaerobic process convert organic wastes to methane and carbon dioxide in the absence of oxygen. Anaerobic treatment has the ability to perform the following decompositions: |
|
 |
Hydrolysis : |
A breakdown of suspended organic solids into soluble organic compounds. |
 |
Acetogenesis : |
First step in anaerobic decomposition where propionic acid is reduced to acetic acid. |
 |
Methanogenesis : |
Second step in anaerobic decomposition where acetic acid is further reduced to methane and carbon dioxide. |
|
There are five(5) processes required in a complete industrial bio system: |
 |
Pre-Screening : |
To remove solids from the waste stream. |
 |
Anaerobic Treatment : |
Or a breakdown to a septic condition. Partial breakdown to methane, carbon dioxide, cellular material and organic compounds. |
 |
Aerobic Treatment : |
A reduction of 95% B.O.D. A complete breakdown to carbon dioxide and water. |
 |
Clarifier : |
Removal of active bacteria and other suspended solids. |
 |
Effluent Disinfection : |
Oxidation of pathogenic bacteria and viruses. |
|
|
|
Universal Advanced Bio-reactor
Advanced Wastewater Treatment System |
|
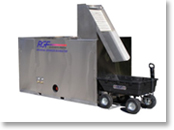 |
|
The Universal Advanced Bio-Reactor is a closed- loop recycle system designed to treat, filter and deliver the cleanest and safest wash water for re-use at your wash bay. The system contains minimal moving parts and replaceble components, low consumables usage and no chemical or microbe addition. The Universal Advanced Bio-Reactor has a small footprint and is totally enclosed for outdoor use and is constructed of all non-corrosive materials. Includes a hand or machine towable grass cart with dump feature. |
|
APPLICATIONS |
FEATURES |
|
|
Golf Courses |
5* more efficient bio-reactor |
Landscape Maintenance |
Counter Current Advanced Oxidation System |
Agriculture |
Oil/ Water Separation & collection |
Universities |
Flow rates Up TO 40 gpm |
Government Facillties |
High Pressure Delivery Pump |
Sod Farm |
Self Cleaning Grass Separation |
Resorts |
Low Maintenance and Operating Costs |
Camp grounds |
Easy Installation |
|
|
Specifications |
|
|
Dimensions |
Unit 58” W x 118” L x 98” H
Grass Cart 33” W x 53” L x 29” H |
Weight (Dry) |
1.600 Lbs |
Filtration |
25 Micron |
Processed Water Storage |
400 gallons |
Delivery Rate |
20gpm @50psi UAB20 40gpm UAB40 |
|
|
|
RGF Bio Ox System
Advanced Grease and Odor Treatment System |
|
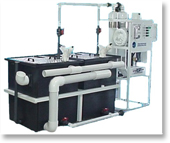 |
|
Bio Ox Mod
A three-part modular system designed to fit through a standard 36” door opening that can be handled with a standard hand dolly for easy delivery into existing basements. The unit has two fludized bed reactors and one clarifier chamber, automatic bacteria feed system, a continuous duty Advanced oxidation gas aeration and odor control system, and an oxidation purge system. Also, a separate photohydroionzation cell for lift-station airbome bacteria and odor control. This system is ideal for hotel basement lift station / grease trap replacement or enhancement. It provides an advanced grease digestive system and advanced oxidation gases for the lift station for odor, bacteria and FOG control. |
|
Specifications |
|
|
Rating |
5 gpm |
Fresh water supply |
1/4” 0.16 gpm |
Fresh water treatment |
carbon |
Advanced Oxidation |
Photohydroionization |
Media Bed |
Multi Poly |
Bacterial Feed |
slow release Bio Tablets |
Oxidation Purge |
RGF Oxy Crystals |
Odor Control |
RGF Turbozone |
Inlet / Outlet |
4” |
Dimensions |
32” * 32” * 36” (Tanks)
18” * 24”* 40” (AOT unit) |
Material |
Polyethylene PVC
Aluminum |
|
|
|
Lift Station Bio Ox |
|
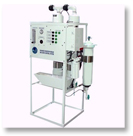 |
|
A compact unit designed to easily fit into the smallest of lift stations with a 24” * 24” footprint. This unit pumps advanced oxidation gases and automatically feeds bacteria into the existing lift station water. A separate photohydroionization cell provides ongoing odor and airbome bacteria control in the room. Lift station grease is physically, chemically and biologically broken down and freely washes away as liquid and gas. Lift station room odors and airbome bacteria are controlled. |
|
Specifications |
|
Rating |
Up to 750 gallon lift station |
Fresh water supply |
1/4” 0.16 gpm |
Fresh water treatment |
carbon |
Advanced Oxidation |
Photohydroionization |
Bacterial Feed |
slow release Bio Tablets |
Oxidation Purge |
RGF Turbozone
|
Odor control |
4” |
Inlet / Outlet |
each 24” * 24” * 70’ |
Dimensions Reactor |
32” * 32” * 36” (Tanks)
18” * 24”* 40” (AOT unit) |
Material |
Aluminum & PVC |
Gas Dispersion |
2” PVC |
|
|
|
Oil Water Separators |
|
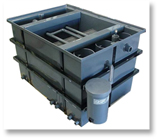 |
|
This section covers coalescing oil/water separation. The concept of a basic gravity oil/water separator is simply a tank vessel that stalls the flow rate to permit gravity to separate oil from water. Oil, having a lower specific gravity than water, will naturally float on water if given time to separate. RGF’s Oil Water Separators are designed to process wastewater containing free oils. The patented systems utilize over five technologies to remove and store the free oils before discharge for reclaim or sanitary sewer. |
|
Specifications |
|
Flow Rate |
OWS-20: 20 gpm OWS-50: 50 gpm |
Dimensions |
OWS-20: 26”W * 50”L * 46”H OWS-50: 76’W * 56”L * 54”H |
System Capacity |
OWS-20: 180 gallons OWS-50: 550 gallons |
Free Oil Capacity |
OWS-20: 7 gallons OWs-50: 7 gallons |
Separation Type |
1/4” lnclined Tube Coalescor, Gravity Separation, Micro-Matrix Coalescors |
Materials |
Polyethylene / Polypropylene / PVC |
Options |
RGF OWS Bio-Disks for oil reduction |
|
|
|
Model SD 1
Sewer Discharge Oil Water Separators |
|
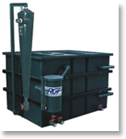 |
|
RGF’s Sewer Discharge Systems are designed to collect contaminated source water, which typically contains petroleum hydrocarbons, heavy metals solid and cleaning fluids. The collected water is processed through the systems and contaminants are removed utilizing over 12 technologies prior to discharge to sewer. |
|
Specifications |
|
Flow Rate |
30 gpm |
Dimensions |
76”W * 56”L * 84” H |
System capacity |
850 gallons |
Free Oil Capacity |
7 gallons |
Separation Type |
1/4” Inclined Tube Coalescor, Gravity Separation, Micro-Matrix coalescors, Multi-Media
Absorption |
Final Filtration Media |
638 Ibs. Multi-Media
Multi-Media consists of Activated Alumina, Carbon, Activated Carbon, Volcansorb Rock |
Oxidation System |
TurboHydrozone (XL only) |
Materials |
Polyethylene / Polypropylene / PVC |
Options |
RGF OWS Bio-Disks for oil reduction Coalescing Centrifugal Separtor (XL only) |
|
|
Evaporation Systems RGF Thermo Oxidizer
Wastewater Advantages |
|
The Thermo Oxidizer System completely oxidizes water borne waste streams, leaving only a dry powder as the residual waste material. Unlike evaporators, the Thermo Oxidizer completely eleminates the water content of the liquid waste. The unit eliminates the typical evaporator problems of corrosion, foaming, residual slurry, V.O.C. emissions, and difficult to clean evaporator chambers. |
|
THE CONCEPT |
|
The RGF Thermo Oxidizer is a designed to completely oxidize liquid waste, leaving only a dry ash residue. By automatically controlling the fuel modulation and the waste flow, maximum efficiency is achieved resulting in a fuel cost as low as $0. 10 per gallon. RGF utilizes a cast ceramic refractory for all interior combustion surfaces to eliminate corrosion and metal failure. By utilizing an optional waste oil burner, the system can eliminate both waste oil and wastewater. |
|
The Thermo Oxidizer was designed by RGF to completely oxidize liquid waste, leaving only ash to dispose. The unit meets NFPA Fire Safety Code requirements.
Unlike a stainless steel evaporator, the Thermo Oxidizer is not subject to chloride stress crack corrosion. It is easily cleaned and requires little maintenance. The biggest difference is the total removel of water content by the Thermo Oxidizer. The wastewater does not accumulate, making it impossible for the wastewater to concentrate. This is an operational asset in that the emissions are not permitted to worsen with time, as they are with an evaporator.
Typical temperature setting range from 800 to 1,400F. Incinerators operate between 1,800 and 3,000F. The Thermo Oxidizer works to thermally decompose chemicals within the wastes to their primary combustion products of Co2, H2O and simple compounds. At temperatures of 700C, Most Chemicals are boken down into smaller molecular weight constituents, and at temperatures of 1000C, the majority of wastes are reduced to ash.
Types of waste streams applicable for treatment by the Thermo Oxidizer are : |
|
Petroleum Hydrocarbon Waste |
RO,NF,UF Concentrators |
Floor Scrubber Waste |
Die Casting |
Tumbling Solutions |
Plating Solutions |
Alkaline Cleaners |
Waste Haulers |
Textiles |
Machinery wastes |
Process Wastewater |
Heavy Equipment |
Compressor Wastes |
Printed Circuit Board Waste |
Food Processing |
Ink and Paint Waste |
Tanker Cleaning |
Manufacturing Processes |
Electro Polishing Rinse Waters |
Diesel Injector Cleaning |
Oil Field Tool Cleaning |
|
|
RGF Thermo Oxidizer
Model To - 150 (150 gph) |
|
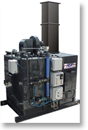 |
|
Specifications |
|
Fuel |
NG or LP |
Dimensions |
10’ 6”L * 6’D * 8’ - 10”H |
Electrical Requirements |
120 VAC - 5A - 1 Phase
460 VAC - 10 A- 3 Phase |
Disposable Rate |
Up to 150 Gallons per hour, clean water |
Construcation |
3/16” Steel Plate / Ceramic Lined / S.S. Door |
Air Supply Requirements |
43 SCFM @ 100 PSI |
Typ. Temperature Settings |
800-1,400 F |
Burner Safeguared Control |
UL,CSA Listed, FM And IRI Approved |
Flame Monitor |
Flame Rod |
Exterior Finish |
High Temp. Two-PArt Polyurethane |
Stack Height From Floor |
19’-10” |
|
|
Floc Systems |
|
Contaminants in wastewater often cause the water to appear turbid or colored. These impurities include a suspended and colloidal materials and soluble substances. Because the density of many of these particles is only slightly greater than water, agglomeration of particles into a large floc is necessary in order for them to be removed by sedimentation and filtration. The clarified water then can be either discharged or reused and the settled floc can be collected, dewatered and disposed of as solid waste. |
|
|
RGF ESP Floc Series
Wastewater Encapsulation Treatments Systems |
|
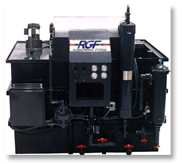 |
RGF’s line of advanced encapsulation treatment systems are fully automatic and capable of treating waste streams contaminated with emulsified oils, solids, heavy metals, ink and paint emulsions, and floor scrubber wastewater. The treated water will usually meet sewer discharge requirements or may be reused for cleaning. The resulting dried sludge from the treatment process normally will pass the TCLP test, which will allow disposal at a non-hazardous landfill. RGF offers a complete line of flocculants modeled to handle any waste stream.
The ESP - 100 series batch Treatment system was designed for versatility and accessibility. It has Post Treatment System intended for applications that require process water disinfection prior to discharge or for re-used of the treated water. The ESP - 100 process up to 200 gallons per hour. |
|
SPECIFICATIONS |
|
|
Batch Time |
½ Hour |
Treatment Capacity |
100 gallons per batch |
Dimensions |
6’H * 7’W * 6” D |
Controls |
PLC controller automated |
Electrical |
220 VAC, 20A 1 Phase |
Add’l Requirements |
compressed air - 100 psi @ 20 scfm |
|
|
*May vary depending on waste stream |
|
|
RGF ESP Floc Series
Wastewater Encapsualation Treatment System |
|
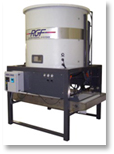 |
|
SPECIFICATIONS |
ESP- 400 |
|
|
Batch Time |
½ Hour |
Treatment Capacity |
400 gallons oer batch |
Dimensions |
12’ H * 8’W * 7’ D |
Controls |
PLC controller automated |
Add’l Requirements |
Compressed Air - 100 psi @ 35 scfm |
|
|
Specifications |
ESP- 600 |
|
|
Batch Time |
½ Hour |
Treatment Capacity |
600 gallons oer batch |
Dimensions |
12’ H * 8’W * 7’ D |
Controls |
PLC controller automated |
Add’l Requirements |
Compressed Air - 100 psi @ 35 scfm |
|
|
|
 |
|
|